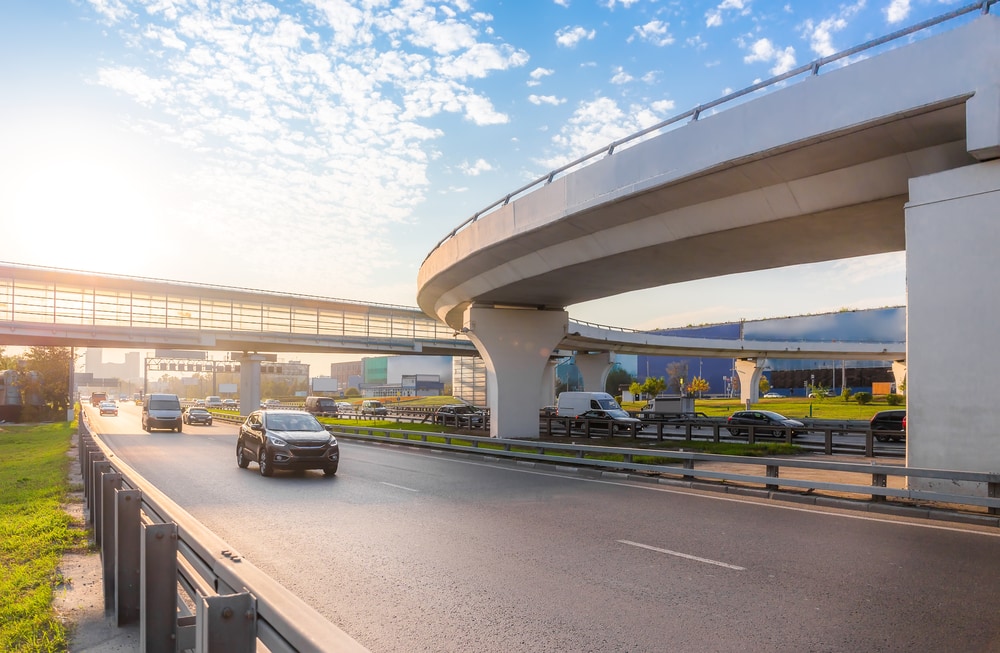
Scott Osterhoudt is LiDAR department manager at ESP Associates, Inc in Charlotte, NC. He’d been at ESP for less than a year when he was asked to take $700,000-worth of mobile scanning equipment out on a small boat and survey a road bridge which was to be converted to a pedestrian bridge. You can imagine he was a little nervous about the boat part! We asked him about the project, how LiDAR helped, and what it’s like to work with TopoDOT.
Who was your customer, Scott?
We were a sub to Cranston Engineering Group in Augusta, GA. They in turn were a sub to Civil Services, Inc (structural) in Jacksonville, FL.
What was project about?
A road bridge more than 90 years old was being converted into a pedestrian bridge by the City of Augusta, GA. There had been abutment issues for many years, resulting in several repairs.
What about the TopoDOT process? Your 3D models look very detailed – how long did it take to extract the topography?
We did a very detailed job, way more advanced than a typical roadway survey would deliver. For example, you wouldn’t normally show every corner of every railing on the bridge – but we did:
A typical traditional roadway survey would involve this: (Total approximately 280 hours) | Field time – 2 weeks involving a 3-man crew of 40 hours per week each, ie 240 hoursDisruption – The work would have involved lane closures, traffic control, PPE, and moreOffice time – 1 week (40 hours)Modeling – None (standard roadway deliverable) |
What we actually delivered with much more sophisticated modelling: (Total approximately 164 hours) | Field time – 3 days made up of: Bathy survey crew – 1 day Static survey crew – 1 day Mobile LiDAR crew (vehicle & boat) – 1 dayDisruption – None (no traffic control or lane closures required)Office time – 3.5 weeks made up of: Processing/registration – 0.5 weeks Extraction – 2 weeks Final mapping, QC and PM – 1 week |
To achieve that same higher-level deliverable using traditional non-LiDAR methods would have involved: (Total approximately 1,160 hours) | Field time – 2 months involving a 3-man crew of 40 hours per week each, ie 1,000 hoursDisruption – The work would have involved lane closures, traffic control, bridge-overhang devices, PPE, and moreOffice time – 1 month (160 hours)Modeling – A similar deliverable. |
How much do you think you saved, compared to conventional surveying methods?
We reckon we saved around 75% compared to delivering the same rich data in the traditional way.
“My personal opinion is that TopoDOT is, by far, the best point-cloud processing company. Part of it is the customer support; I can pick up the phone any time and talk with Ted, Jen or Maury. With other companies, you might get an email reply weeks or months later, if at all. But it’s also so intuitive to use. I’ve taught 30-year surveying veterans to use it in just a couple hours – they’ve literally hit the ground running on day one.”
– Scott Osterhoudt, April 2019
How was the 3D model used by downstream operations?
Civil Services used the data to design an abutment that will support future pedestrian use of the bridge. Cranston used the bridge wall and the bent locations to verify original station/offset locations and tie them to the original design coordinates.
How’d you feel having $700K riding in the boat?
It was scary! I’d not been with the company a full year yet, and here I was in a little boat with all this expensive mobile LiDAR unit. But it all worked out great.
How did you handle the data?
We set mobile LiDAR panels before beginning the surveys. The client surveyed and delivered data in .XYZ format on all panels and control points that matched previous projects on the bridge to ESP. We were able to use mobile control for most of the static scans as well. We did set some additional static control that was out of view of the mobile survey areas.
First, we scanned the roadways with a vehicle-mounted Riegl VMX 1HA mobile scanning system. Then we scanned the side profile of the bridge with both the Leica P40 and a Trimble SX10, and finally we scanned the underside of the bridge using the Riegl VMX 1HA again.
We were able to tie the boat’s mobile LiDAR survey to the vehicle’s mobile LiDAR survey using the point-cloud data from the vehicle mobile LiDAR survey and the static LiDAR surveys. We also conducted a bathymetric survey using a single-beam HydroLite system using a base station and on-board GPS.
What was your customer’s reaction?
The client was ecstatic! They were blown away by the amount of data in the CAD file. It may have been more than they were ready for, but I think we opened their eyes to working in a 3D world.
1 Comment
Cory Lyle · May 23, 2019 at 11:36 AM
Sounds like a fantastic project. Bringing all the different datasets together to create a complete point cloud of the bridge must have been a rewarding and awe-inspiring moment! Would love to see some visuals on how the model turned out. Congrats.